When to Use Magnetic Particle Inspection
Magnetic Particle Inspection (MPI), is a non-destructive testing technique used to detect surface and slightly subsurface flaws in most ferromagnetic materials such as iron, nickel, and cobalt, and some of their alloys.
MPI is a very effective method for locating surface breaking and slight sub-surface defects such as cracking, pores, cold lap, lack of sidewall fusion in welds etc.
There are many different techniques for conducting MPI. The most versatile technique is using a 110v AC hand held electromagnetic yoke magnet. A white strippable paint is applied as contrast background and a magnetic “ink” composed of iron powder particles in a liquid carrier base.
The area is magnetised with the yoke magnet. In the event of a surface or slightly sub surface defect being present, the lines of magnetic force will deform around the defect.
The magnetic ink is applied and the iron powder particles will bridge the gap caused by the defect and give a visible indication against the white contrast background.
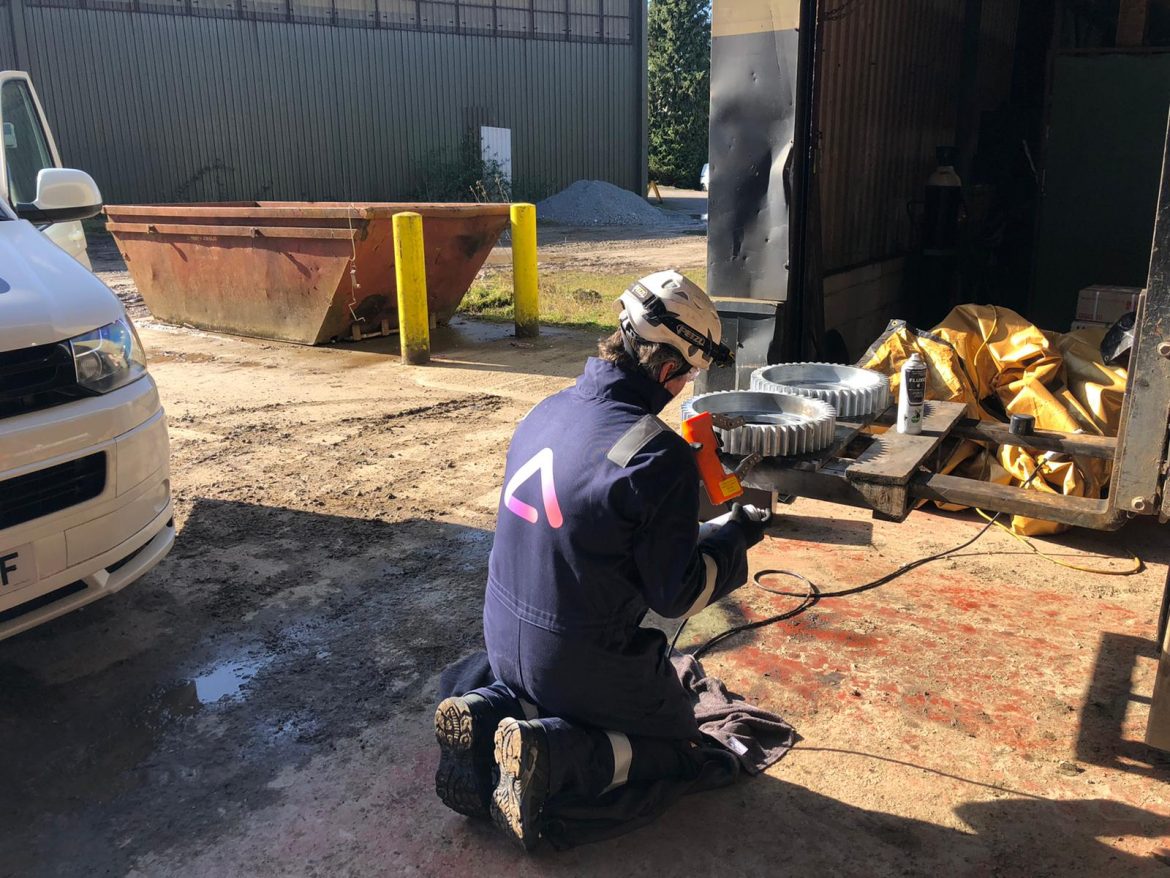
MPI provides very good defect resolution and is used extensively on welded fabrications in magnetic material, castings, locating fatigue cracks in items subject to cyclical stress.