DOW, UK
W911 Cooling Tower sUAS GMISS Inspections
Client: Dow
Location: Wales, UK
Services Required:
GMISS Inspections:
Comprehensive assessment of the structural timbers both externally and internally.
External Structural Inspection:
Evaluation of the seven slats on both sides of the cooling tower.
Internal Structural Inspection:
Detailed inspection of the internal wooden structures without taking the cooling cells offline.
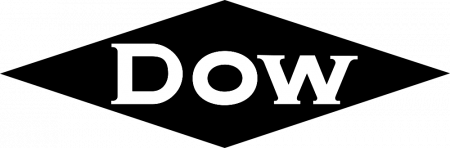
Dow, UK
Introduction
Sutro Group undertook a challenging project to perform Global Mechanical Integrity Safety Standard (GMISS) inspections on the W911 Cooling Towers in Wales. These inspections, essential for assessing the condition of the structural timbers both externally and internally, typically required extensive scaffolding, resulting in significant time and cost expenditures, as well as reduced cooling capacity due to the need for offline cooling cells. By leveraging advanced sUAS (small Unmanned Aerial Systems) technology, Sutro Group offered an innovative solution that eliminated the need for scaffolding, significantly expedited the inspection process, and ensured minimal disruption to the client’s operations.
Benefits and Savings
By conducting the inspections using sUAS, Sutro Group achieved remarkable savings and operational efficiency:
An estimated 3,000 person-life hours were saved by eliminating the need for scaffolding.
Approximately £150,000 was saved in scaffolding costs alone.
The use of sUAS allowed for the cooling cells to remain operational, preventing the potential loss of production rates that would have resulted from reduced cooling capacity.
Project Overview
The W911 Cooling Tower inspections involved complex procedures due to the requirement of taking cooling cells offline and the extensive scaffolding needed to access internal structures. Sutro Group’s approach using sUAS technology transformed this process by providing a faster, more efficient method without compromising the cooling capacity.
Traditional Inspection Challenges
Historically, inspecting the W911 Cooling Towers involved erecting scaffolding to access the internal wooden structures, reducing the cooling capacity by one-third. The exterior inspection was further complicated by the need for substantial scaffolding to reach each level. Areas requiring inspection included the seven slats on both sides of the Cooling Tower and the internal structure, as depicted in the accompanying image.
Innovative Approach
Sutro Group’s utilisation of Dow Approved sUAS technology for GMISS inspections eliminated the need for scaffolding and significantly expedited the inspection process.
Conclusion
Sutro Group’s innovative approach to the W911 Cooling Tower inspections highlights their commitment to efficiency, cost savings, and operational excellence. Utilising cutting-edge technology, Sutro Group not only met inspection requirements but also delivered significant value to Dow, ensuring minimal disruption to their operations.
For more information on how Sutro Group can optimise your inspection processes, contact us today:
0800 069 9395
info@sutrogroup.co.uk
Join our network
Be the first to discover our latest news and job opportunities.
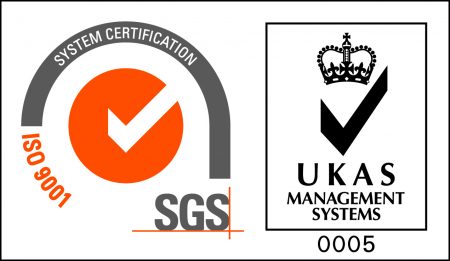
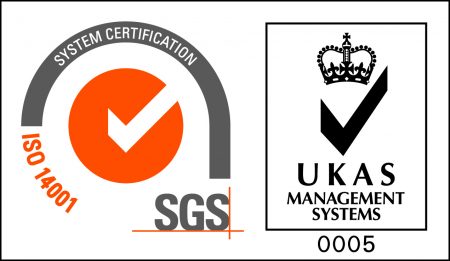
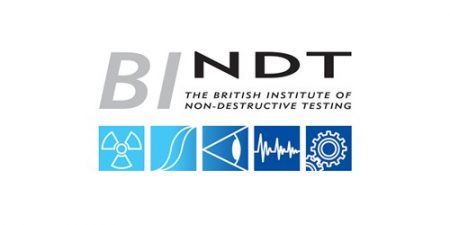
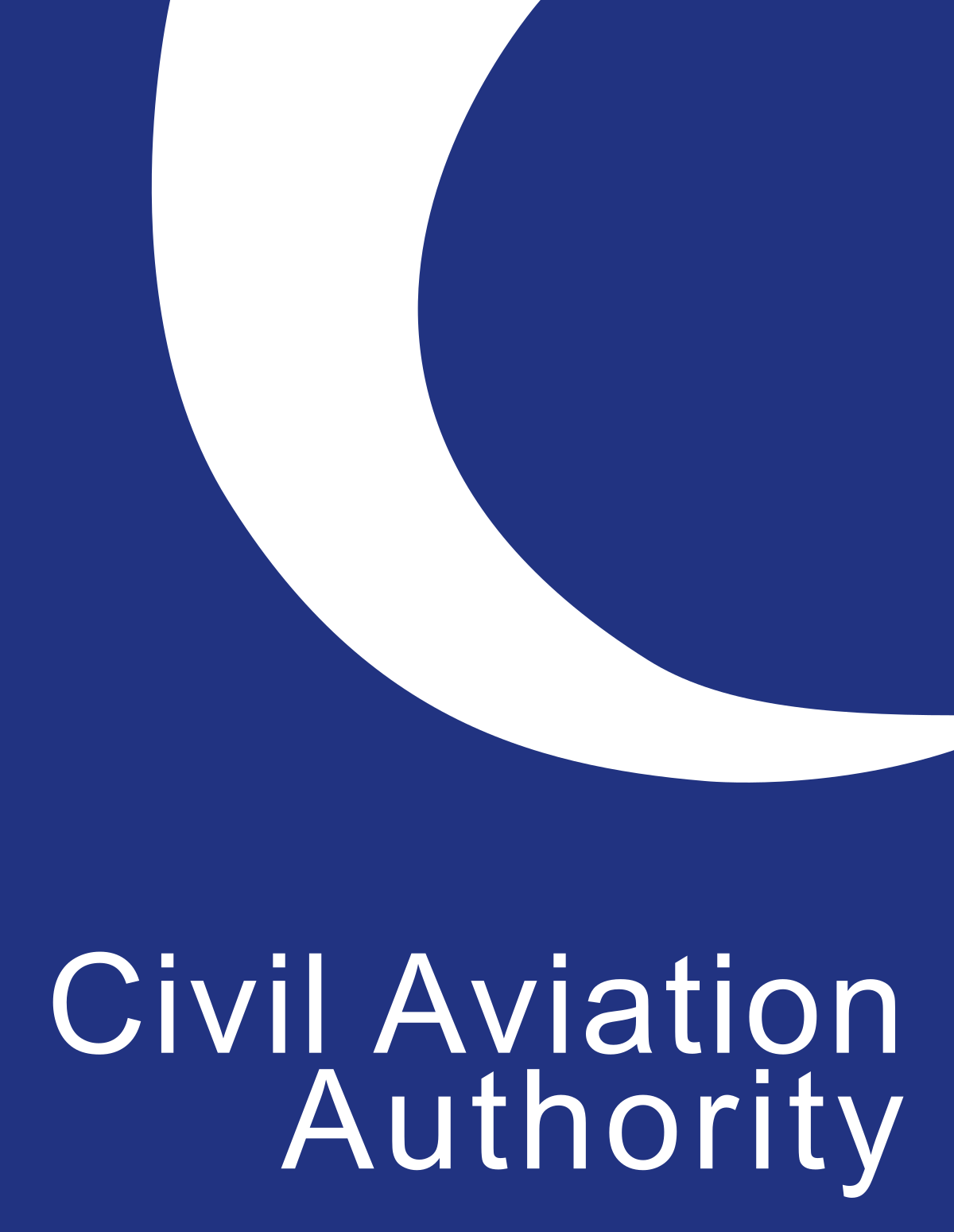
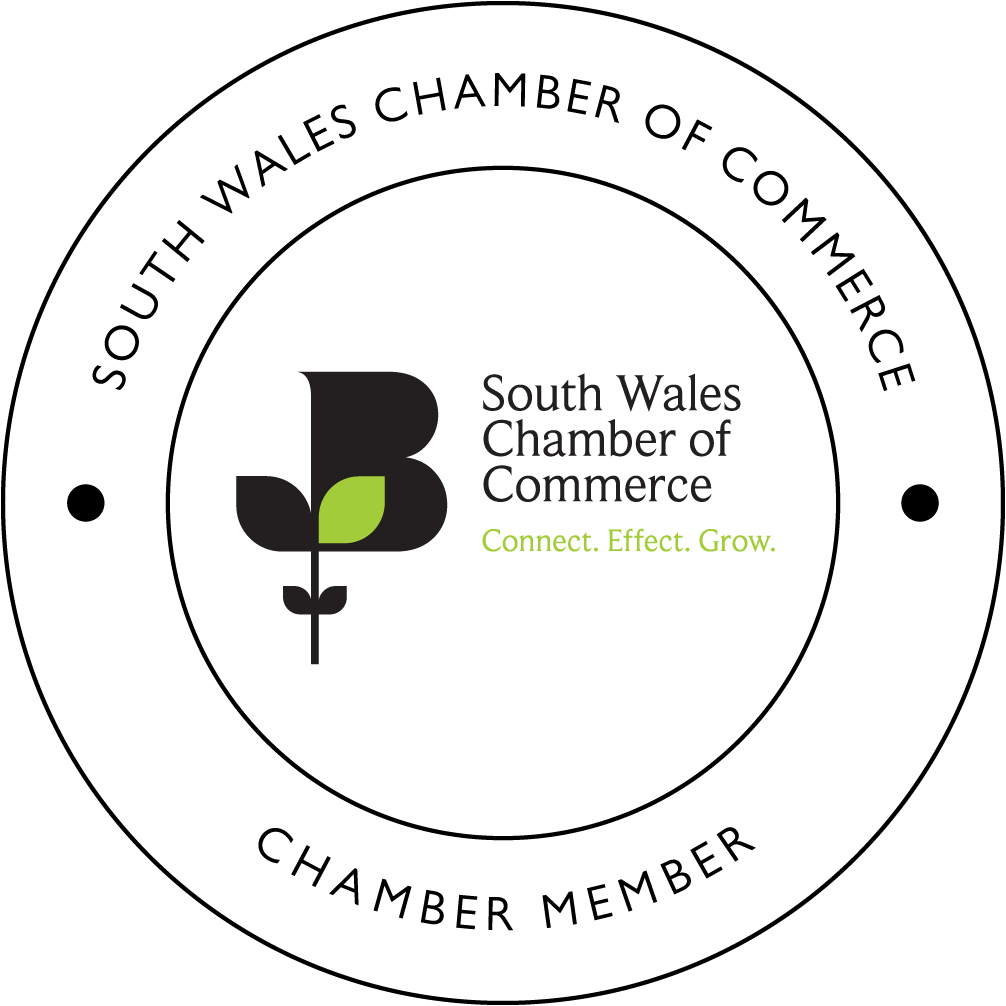
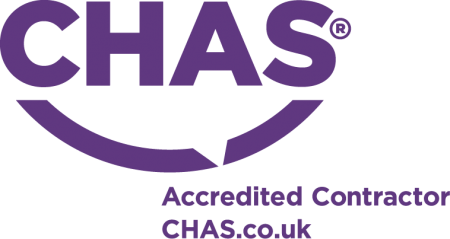